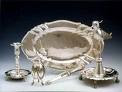
Materials:
Silver Pineapple (99.8%). Copper (wire or plate), bronze (for welding) colored stones (turquoise, quartz, onyx, obsidian, opal, agate, etc..) Solder pastes, borax, sulfuric acid, sodium bicarbonate. Oxides, polishing pastes, cloth, abrasive cloth, lijas. Silver pineapple bought in specialist shops which sell this material. The colored stones are purchased from traders who bring the material of the mines. The other materials are bought in stores.
Equipment and Tools:
Trifiladora, laminator, dies, dies, pliers, pliers, torches, polishing, grinding.
Production Process
Cast:
It melts the silver pineapple with 7.25% copper, the result is 92.5% silver purity poured into molds or blocks for drawing or rolling. This mixture is achieved through a proper malleability, silver 9.25 is ideal for work, otherwise it is hard and brittle.
Annealing: The rods obtained are heated with the torch until red hot, this is done so that the metal is flexible and has greater consistency.
Laminate:
Is passed through a roller to convert the block into thin sheets or plates.
Trifilado:
The plate is passed through the trifiladora threads to make it different sizes, usually used after diamond cubes or rows to accurately gauge.
Preparation:
There are different techniques to prepare the pieces of jewelry, we will describe briefly the most important. .- For this casting molds are used. The mold was initially prepared in rubber, which is the matrix, based on a physical sample. On this matrix is filled wax by multiplying the quantity desired, these are organized into small trees that are introduced within an iron pipe that is filled with special plaster, a rather dry heated to remove the wax, these are the final mold which injected with a molten silver centrifuge. After removing the mold is cut, it Liman joints and gives the finish. The plaster mold is broken because it has a single lifetime. .- The round filigree silver thread 15-25 mm. becomes thin thread. With tweezers are forming the desired figure, weaving threads of silver, then welded on the frame with a silver and bronze chips (mix the solder is 10 parts of silver with 5 bronze). Printing .- This was used as a matrix of steel mold, the matrix is pressed on a silver plate which gives the same figure of the matrix on a silver plate, then cut the edges and the figure is refined . Armed manual .- Prepare the frame with silver wire and using tweezers, pliers, rulers, will give the desired shape with pieces of metal wire, according to the design to be achieved. Bleaching: the product is bleached by immersing in sulfuric acid and then in a solution of sodium bicarbonate. Finally washed using detergent and water. Preparation of the stones: the stone color (turquoise, quartz, onyx, obsidian, opal, agate, etc..) Is carved with tools equipped with diamond discs and engine types, the cuts are made of stone and then wear until the model eventually becomes the mark to tie and polished with sandpaper, abrasive cloth and with cloth impregnated with polishing paste. Crimp: Are located and holding the stones of color, properly prepared, within the frame of silver. Grinding and polishing: Is polishing and polishing with emery cloth placed on rubbing with a paste and rinse.